MANUFACTURING
2024/05/16
Efficiently Manufacturing Eco-Friendly Aircraft Components with CFRTPs | Initiatives for Decarbonization in the Aviation Field
- Interview
- Aircraft
- Aerospace
- Technology
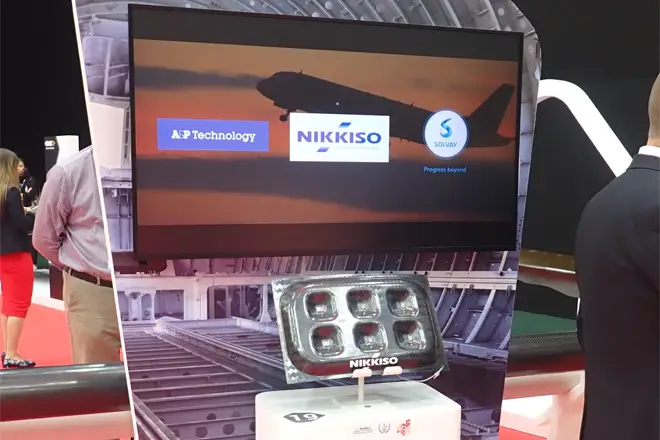
Index
As in other fields, the 2022 long term goal in the aviation field is to achieve carbon neutrality by 2050, and initiatives toward decarbonization, including legal revisions and the formulation of basic policies, are being promoted and accelerated.
Amid this situation, carbon fiber reinforced thermo plastics (CFRTPs) are increasingly attracting more attention as a material that can reduce the aircraft manufacturing field’s impact on the environment.
We interviewed Mr. Saito, who is in charge of research and development of CFRTP molding technology at Nikkiso. From the perspective of reducing the impact on the environment, we asked in detail about the characteristics of CFRTPs and the molding technology established by Nikkiso.
Koichiro Saito: Joined Nikkiso in 2020 after being engaged in development and design of automotive engine components. In charge of research and development at the Technology Department, the Technology Center, the Aerospace Division. |
Expectations of CFRTPs as the next-generation structural material are growing
――Thank you very much for your participation today. First of all, could you give us an overview of CFRTPs.
Saito: First of all, the structural materials used for aircraft have shifted from metals to carbon fiber composite materials in order to reduce weight. There are two types of carbon fiber composite materials: CFRPs*1, which use thermosetting resin to which carbon fiber is added as a reinforcing material; and CFRTPs*2, which use thermoplastic resin to which carbon fiber is added. Currently, CFRPs are the mainstream structural material of aircraft. CFRPs use thermosetting resin, which hardens when heated, while CFRTPs use thermoplastic resin, which softens when heated. A characteristic of CFRTPs is that their shape can be changed freely by applying heat even after they have hardened.
It’s easier to understand if you imagine that CFRPs are like a cookie, whose shape cannot be changed once baked, and CFRTPs are like chocolate, whose shape can be changed depending on the temperature.
*1:CFRP=Carbon Fiber Reinforced Plastics
*2:CFRTP=Carbon Fiber Reinforced Thermo Plastics
――Why are CFRTPs attracting attention as environmental awareness increases in the aviation field?
Saito: One factor may be that thermoplasticity means higher recyclability. As I mentioned earlier, CFRTPs are a thermoplastic material. Since the shape of used components can be changed by applying heat, they can be reused for other components. We do not need to dispose of used components, and we can save resources. For this reason, there are growing expectations regarding research and development on this material.
In the case of conventional CFRPs, we need to prepare a cryogenic environment at -20°C to prevent the resin from hardening during storage. Even in such an environment, a chemical reaction occurs little by little and hardening progresses. So, there is an expiration date by which CFRPs can be used as a material.
However, CFRTPs can be stored at room temperature without any changes in condition, and demonstrates its performance as a material in a room temperature environment. Because we do not need to prepare a special freezer or manage expiration dates as is the case with CFRPs, we can cut management costs significantly. Another factor in CFRTPs attracting attention may be that their storage does not require electricity or other energy.
――Are they superior to conventional structural materials in terms of sustainability.
Saito: Yes. Moreover, if a part of a molded component is softened by applying heat, it can be "welded" to another component without bolts or adhesives, in the same way as metal welding. This improves production efficiency. In addition, not having to use bolts reduces weight, which leads to a reduced airframe weight resulting in improved fuel efficiency, and reduced CO2 emissions through a reduction in the energy required for manufacturing. These features are unique to CFRTPs.
――Given these characteristics, where are CFRTPs used?
Saito: Although CFRTPs have begun to be adopted in some components for aircraft and automobile bodies, they have not yet been utilized to the extent that they replace CFRPs, which are said to account for 50% of the weight of airframes.
――Why are CFRTPs currently not utilized very much?
Saito: The largest reason is technical hurdles to molding. While the molding temperature of CFRPs is about 120°C to 170°C, the molding temperature of some types of high-performance CFRTPs required for aircraft is 400°C. They are very difficult to mold because temperature and pressure must be kept uniform in order to prevent differences in the temperature and pressure of the materials in the mold at this high temperature.
In addition, since the molding temperature is high, when using a conventional autoclave that can easily control temperature and pressure the subsidiary materials and equipment used for molding must also be able to endure high temperature. This tends to increase the cost burden compared with CFRPs. I think it is another reason why the adoption of CFRTPs is slow.
Lowered the impact on the environment and significantly reduced the manufacturing lead time. Establishment of proprietary molding technology for CFRTPs
A CFRTP integrated high-rigidity structural member
――I understand that Nikkiso has established proprietary molding technology for CFRTPs and has been selected as a finalist in the JEC Composites Innovation Awards 2023 (*) for its aircraft component development project. First, please give us an outline of the project.
(* JEC Composites Innovation Awards: Sponsored by the JEC Group, a media and event organization. Awards to reward collective cutting-edge, creative projects which demonstrate the full potential of composite materials / Reference: JEC; The JEC Composites Innovation Awards: 2023 official finalists line up)
Saito: This project was started by Nikkiso in 2020 as part of the development of aircraft components utilizing CFRTPs.
In order to produce light and strong panel-shaped components from thermosetting materials such as CFRPs that have excellent strength, rigidity and shock absorption, it is common to use honeycomb materials (beehive-shaped reinforcements). Honeycomb materials are frequently used for aircraft components such as flooring and various aircraft panels. However, such honeycomb materials have some problems, including high costs and difficulty in processing with high accuracy.
In this project, as part of the research and development we had been working on with the theme of creating light and strong aircraft components without using expensive honeycomb materials, we devised reinforcement panels for aircraft primary structural components that could withstand loads from various directions. We won the award by realizing a molding method with a lower environmental impact and reduced manufacturing lead time.
――What are the characteristics of the molding technology established by Nikkiso?
Saito: The key point is that we established a press molding method for complex-shaped panels with a method that increases strength by using carbon fibers in a continuous state, instead of cutting them into pieces, while reducing the impact on the environment and the manufacturing lead time.
The autoclave molding method, which Nikkiso has adopted for CFRP molding, performs molding by applying pressure and heat using a pressure vessel called an autoclave.
This method typically takes about 4 to 10 hours to mold a CFRP component (depending on the type and shape of the carbon fibers), and is not suitable for CFRTPs, which require a higher molding temperature. In addition, CFRTP molding does not require a high temperature to be maintained for a long period of time, because no chemical reaction is involved.
In contrast, with the press molding method we developed, sheet-shaped material is placed between an upper and lower mold, the upper and lower mold are closed, and then heat and pressure is applied. This method forms components by quickly softening the material with the molds heated to a high temperature, and cooling the material immediately to obtain a molded product. It works well with CFRTPs, and has successfully reduced the lead time for manufacturing components to about one seventh.
Another feature of the press molding technology developed by Nikkiso is that, in addition to reducing the molding time, it reduces waste and production costs.
――How much does the press molding method established by Nikkiso reduce molding waste compared with conventional methods?
Saito: While the molding of components with the autoclave molding method requires many subsidiary materials such as film and adhesive tape to create a vacuum, the press molding method only uses molds. The method emits almost zero waste from manufacturing, which is also a benefit to the environment.
In both the autoclave molding method and the press molding method, it is common to mold a component in a slightly larger size and then trim its outer shape. In contrast, the molding technology established by Nikkiso is characterized by the fact that not much trimming is required after molding and waste and manufacturing costs are reduced, since it employs a technique that can mold a component in the exact size.
――What challenges should be solved for commercialization?
Saito: Since we are still in the testing phase, we would like to first focus on producing components more quickly and with stabler quality for mass production. And then we would like to expand the range of the technology by making it possible to mold components of shapes and sizes different from the reinforcement panels we made this time.
――I heard that a CFRTP integrated high-rigidity structural member (panel for reinforcing the blocker door) manufactured by Nikkiso's proprietary press molding method was exhibited at JEC World 2023 in Paris held from April 25 to 27.
Saito: Yes. As a finalist of the JEC Composites Innovation Awards 2023, we exhibited our molded products at a booth set up by the organizer. We also exhibited our products at the booths of our project partner companies, SOLVAY and A&P Technology, respectively.
They attracted a lot of attention as they were displayed in the most prominent place of each booth thanks to us being selected as a finalist. When we exchanged opinions with people from aircraft manufacturers, we received many positive opinions.
Also, since it is a technology under development and still in its infant stage, we received a lot of advice on specific steps to be taken toward the future, which was an opportunity to realize that there were expectations regarding our technology.
Combining our proprietary technologies to create components only we can create
――Thank you very much. Finally, please review the research and development so far and tell us what the Technology Department of Nikkiso wants to realize.
Saito: For Nikkiso, which has been manufacturing CFRP components using the autoclave molding method for 40 years, this project was a major challenge to acquire new manufacturing technology using new materials.
We successfully formed components by repeated trial and error, and as a result, we were selected as a finalist in the JEC Composites Innovation Awards 2023. We are very pleased with this achievement. It gave us confidence that we were taking on the challenge of something interesting.
From now on, while we will improve the technology toward mass production and the adoption of CFRTP components as a matter of course, we will also establish the welding technology Nikkiso has been working on independently and combine it with the technologies Nikkiso has cultivated so far to create components that only we can create.
Pickup
-
MANUFACTURING
Pumps also actively used in semiconductor manufacturing: 20 years of history of compact, high-speed canned motor pumps
- Technology
- Interview
- Pump
- Semiconductor
2025/05/21
-
MANUFACTURING
Nikkiso's DX initiatives: CAE Support Department continues to evolve, aiming to eliminate dependence on the skills and expertise of specific people
- Technology
- Interview
2025/04/09
-
MEDICAL FIELD
A region on the forefront of dialysis treatment: Nikkiso automation gathering attention in Europe
- Medicalbusiness
- Hemodialysis
- Interview
2025/03/13
関連記事
-
MANUFACTURING
Pumps also actively used in semiconductor manufacturing: 20 years of history of compact, high-speed canned motor pumps
- Technology
- Interview
- Pump
- Semiconductor
2025/05/21
-
MANUFACTURING
Nikkiso's DX initiatives: CAE Support Department continues to evolve, aiming to eliminate dependence on the skills and expertise of specific people
- Technology
- Interview
2025/04/09
-
MANUFACTURING
Behind the development of the 3D Sinter, a new technology which serves to improve both the quality of SiC power semiconductors and productivity in the manufacturing process
- Semiconductor
- Interview
- Technology
- Industrial
2025/02/19
-
MANUFACTURING
What are the characteristics of technical jobs at companies? What are Nikkiso’s strengths in particular? | Answers to questions from students
- Industrial
- Pump
- Interview
- Technology
2024/09/19