MANUFACTURING
2025/05/21
Pumps also actively used in semiconductor manufacturing: 20 years of history of compact, high-speed canned motor pumps
- Technology
- Interview
- Pump
- Semiconductor
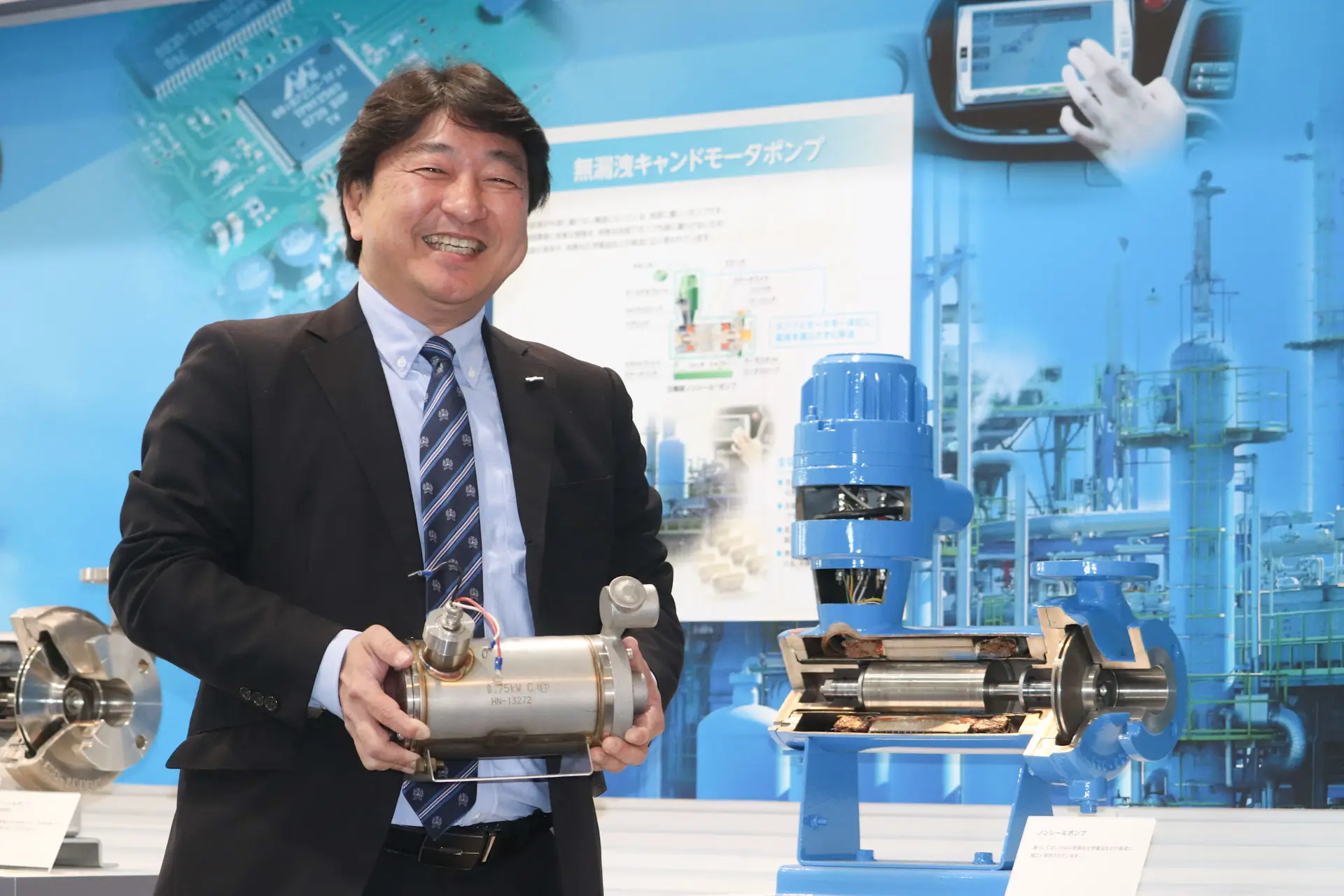
Index
Nikkiso pumps are also playing an active role at manufacturing sites for semiconductors, a market that is expanding.
This compact, high-speed canned motor pump (CMP) was developed about 20 years ago. Initially designed for plastic product manufacturing sites, sales were lackluster. At one point, the company was on the verge of discontinuing the manufacturing of this product. It was five years after development took place that the company began to capture demand for use in semiconductor manufacturing. The compact, high-speed CMP, which was on the verge of collapse, suddenly changed course and demand increased in the semiconductor market, because the technology that its developers had poured into it was recognized.
Masatake Hattori, Fellow of the Industrial Division, who was involved in the development of the product, looks back on 20 years of pioneering new markets through the taking on of the challenge of implementing miniaturization and higher speeds. *Affiliations and titles are current as of the time of the interview. |
No leakage for expensive coolant medium" - growing demand in the semiconductor market
—— First of all, can you tell us where in the semiconductor manufacturing process compact, high-speed CMPs are used?
Hattori: One of the front-end processes in semiconductor manufacturing is dry etching. It is a process involving the use of things like reactive ion gas or plasma gas to scrape a thin film covering the surface of a substrate called a silicon wafer in order to create integrated circuits on the substrate.
Since the substrate heats up when dry etching is performed, the worktable must be cooled by circulating coolant using a thermostatic device. Nikkiso's compact, high-speed CMP pumps are used for pumping that cooling liquid. The pumps are built into thermostatic devices, which are crammed with piping. As such, the size of the pumps is quite small, measuring only about 40 cm in size.Compact, high-speed CMP in the front with a general CMP in the back
—— Why are Nikkiso pumps used?
Hattori: Fluorine-based inert liquid is circulated as the cooling liquid. This is an expensive liquid, costing tens of thousands of yen per liter. In addition, efficient cooling is required to prevent loss from occurring due to leakage. That is why people choose to go with Nikkiso's CMP, because the pump and motor are integrated into a single structure, which prevents the leakage of liquid.
Nikkiso's first compact pump, realized through high-speed rotation technology
—— How did you develop the compact, high-speed CMP?
Hattori: We developed it about 20 years ago. Until then, Nikkiso's CMPs had been delivered to the petrochemical and chemical industry markets in large, sturdy containers with explosion-proof specifications. Apart from these conventional CMP, we wanted to incorporate new technologies to create smaller pumps. We thus decided to take on technological challenges.
—— Are there any benefits to making the pump more compact?
Hattori: A more compact size would result in an expanded market because it can then be installed within equipment where CMPs of the past could not be. As a customer, a smaller pump would also serve to eliminate wasted space and lead to an overall impact in terms of costs. Therefore, we believed there was a need for "smaller size and higher speed".
—— What were some of the challenges you faced in the development process?
Hattori: Simply reducing the size does not result in achieving the target flow rate and pressure. We incorporated faster pump motor rotation to ensure the required motor output and obtain the target pump flow rate and pressure. Doubling the pump motor rotation speed reduces the overall volume to about one-fourth.
However, higher rotation speeds mean that a larger burden is placed on the bearings. This was addressed by taking into consideration elements such as the compatibility of the bearing material and the shaft side material as its counterpart.
With not much popularity gained in the plastics market, the product faced once in danger of a discontinuation of sales
—— So, you developed a compact, high-speed CMP, which is quite difficult to develop. Then, you tried to market it for semiconductor manufacturing, right?
Hattori: No, that was actually not the case. It was not originally developed as a pump for semiconductor manufacturing. We were aiming to have it geared toward plastic product manufacturing equipment. Plastic products are manufactured by heating and melting a particulate plastic material referred to as "pellets," which are then injected into a mold and cooled. The temperature controller is a system that regulates the temperature by running hot oil or hot water through this mold. The product was intended to be used as a pump installed within the temperature controller.
There were many plastic product manufacturers who were looking to mass produce products using plastic injection molding. So, we thought that if we could mass produce a pump that was smaller than those already on the market, there would be a need for it.
—— Was there actually any customer demand for the product?
Hattori: Unfortunately, we could not get many orders. This is because the cost involved was higher than expected, which resulted in the selling price becoming higher. Our salespeople tried hard to sell the product to customers, but customers kept saying that it was too expensive.
Amid a situation where we were unable to successfully expand our sales channels for products geared to temperature controllers, I myself was seconded to a subsidiary in Germany from 2005 to 2010. While I was on assignment there, I received phone calls from Japan asking if they could stop selling the product. I too had given up on continuing with the manufacturing of the product.
Subsequently, however, the situation took a significant turn for the better. The impetus for this was our foray into the semiconductor industry as we sought new customers. Sales then grew, and the compact, high-speed CMP turned into a hit product.
The limelight had shone on the technology which those involved had poured their hearts into, and that's why "pump development is interesting."
—— The fact that you received inquiries from customers in a market other than the one that was originally envisioned, must have meant that there were people who appreciated the technology.
Hattori: As I mentioned earlier, the cooling liquid used in semiconductor manufacturing is a very expensive liquid, costing several tens of thousands of yen per liter. However, someone who saw the value of small, high-speed CMP and said, "I'll pay the high price if it can be incorporated into the equipment and prevents leakage," was in a different industry than the plastics industry that we were initially aiming for. Our senior salespeople kept their antennae up and steadfastly came up with a sales plan, and on top of that, our junior engineers improved the first machine to meet the detailed needs of our customers. That's how it happened, and that's why it's selling so well today.
—— How did it feel to finally see sales increase as a result of having taken on a technical challenge?
Hattori: Looking back, I wonder if we were ahead of our time. The results of our having undertaken the challenge of making a product "smaller and faster" more than 20 years ago are now catching up with the business situation we are seeing. At first, the product did not sell at all. But I now know that I was not wrong in my expectation that there was a need for small pumps. It is a great honor for an engineer to receive requests from customers in this way.
—— Is the know-how involved in miniaturization and the implementation of higher speeds being utilized for liquefied hydrogen pumps for hydrogen aircraft, which are products for which you have announced the successful completion of actual liquid tests?
Hattori: Aircraft parts must be compact and lightweight. Liquefied hydrogen pumps for hydrogen aircraft have also been made more compact and lighter by making rotation happen at high speeds. Considering the characteristics of hydrogen as a liquid, it was necessary to significantly increase the rotation speed when compared to conventional compact, high-speed CMPs. Thus, a further leap forward was required while building on existing technology. However, Nikkiso has always been good at high-speed rotation and has a proven track record. So, there was no resistance in terms of taking on the challenge of a new "smaller and faster" product.
Press Release: "Success in performance testing of a liquefied hydrogen pump for hydrogen aircraft" |
—— What do you find interesting about the area of pump development after being involved in it for so many years?
Hattori: I feel the real thrill of development when I take on a challenge involving something that no one has done before, and the customer ends up pleased with the product that has been delivered to them. While there were many failed attempts at coming up with a product, that is how our final product ended up seeing the light of day. We can make new products with the technology we have cultivated thus far. The development of pumps is indeed an interesting endeavor.
Pickup
-
MANUFACTURING
Nikkiso's DX initiatives: CAE Support Department continues to evolve, aiming to eliminate dependence on the skills and expertise of specific people
- Technology
- Interview
2025/04/09
-
MEDICAL FIELD
A region on the forefront of dialysis treatment: Nikkiso automation gathering attention in Europe
- Medicalbusiness
- Hemodialysis
- Interview
2025/03/13
-
MANUFACTURING
Behind the development of the 3D Sinter, a new technology which serves to improve both the quality of SiC power semiconductors and productivity in the manufacturing process
- Semiconductor
- Interview
- Technology
- Industrial
2025/02/19
関連記事
-
MANUFACTURING
Nikkiso's DX initiatives: CAE Support Department continues to evolve, aiming to eliminate dependence on the skills and expertise of specific people
- Technology
- Interview
2025/04/09
-
MANUFACTURING
Behind the development of the 3D Sinter, a new technology which serves to improve both the quality of SiC power semiconductors and productivity in the manufacturing process
- Semiconductor
- Interview
- Technology
- Industrial
2025/02/19
-
MANUFACTURING
What are the characteristics of technical jobs at companies? What are Nikkiso’s strengths in particular? | Answers to questions from students
- Industrial
- Pump
- Interview
- Technology
2024/09/19
-
MANUFACTURING
Efficiently Manufacturing Eco-Friendly Aircraft Components with CFRTPs | Initiatives for Decarbonization in the Aviation Field
- Interview
- Aircraft
- Aerospace
- Technology
2024/05/16