くらしを豊かに
2023/02/27
脱炭素・EVの普及に欠かせないSiCパワー半導体とは?基礎知識や今後の展望を解説
- 脱炭素
- 技術開発
- 半導体
- インダストリアル事業
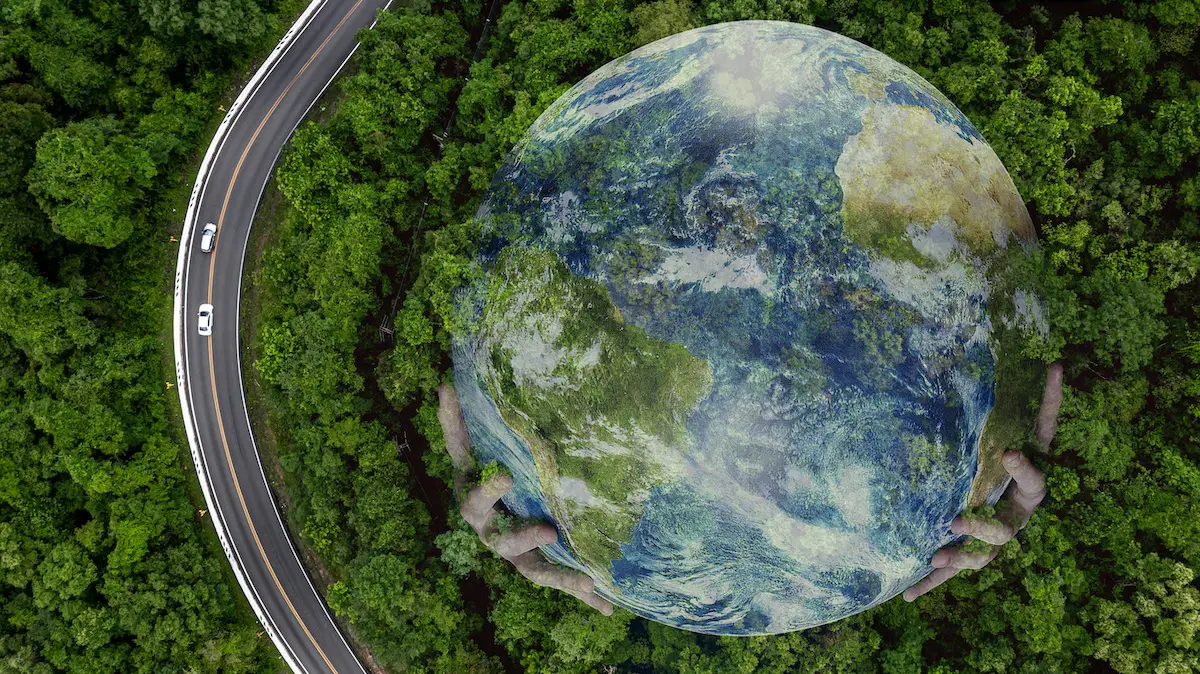
目次
気候変動問題の解決が世界共通の課題とされ、脱炭素化に向けた動きが加速する今。
IEA「Net Zero by 2050」によると、世界の二酸化炭素の約2割は運輸部門から排出されており、その内自動車業界が約4分の3を占めています。
脱炭素を実現するためには、自動車業界における脱炭素化が必須と言われ、EV(電気自動車)の開発・普及を目指す取り組みが進められています。
(参照:IEA「Net Zero by 2050」、https://www.iea.org/reports/transport)
こうした動きを背景に、今需要が大きく拡大し注目を集めているのが「SiC(炭化ケイ素)パワー半導体」です。今回はこのSiCパワー半導体について、役割や特徴などの基礎知識から市場動向、さらに開発の状況と展望まで、詳しく解説します。
脱炭素の実現に向けて高まるEV需要
気候変動の深刻化を受け、その大きな要因の一つである温室効果ガスの排出を全体としてゼロにすること=「脱炭素化」を目指す取り組みが、世界中で行われるようになりました。
脱炭素を実現するためには、家庭や自治体、各産業分野などさまざまなセクターでの取り組みが求められますが、中でも重要な要素の一つになると考えられているのが「自動車」を中心とした運輸部門の取り組みです。
世界各国で動力源の電化を中心とした取り組みが進められる中、「EV(電気自動車)」の開発・普及への期待が高まっています。
国際エネルギー機関(IEA)が発表した「Net Zero by 2050」によると、2050年までに全世界の自動車をネットゼロにするためには、2030年までに世界の自動車販売の60%以上をEVにすることが必要であると言われています。EUでは2035年までにガソリン車やディーゼル車など内燃機関車の販売を禁止する方針が発表されるなど、欧州を中心にEV化が加速しています。
(参照:日本経済新聞「 EU、ガソリン車の新車販売禁止 35年までに」)
EV普及には「パワー半導体」が必要
自動車には、エンジン・ブレーキをはじめとしたあらゆる動きや電力のコントロールを行う役割を持つ「半導体」が使われています。
車載用として使われる半導体にはいくつかの種類がありますが、EVの場合は通常の自動車と比べてより高圧・大容量の電力が必要です。そういった大きな電圧や電流を扱える半導体が求められます。ここで活躍するのが「パワー半導体」です。
パワー半導体は、その電圧や電力への耐性の高さから、自動車だけでなく産業機器、電力、鉄道、家電まで多様な電気機器の制御に用いられています。
このように幅広い場面で活躍するパワー半導体は、開発の積み重ねで性能が高められてきました。しかし、「現在のSi(ケイ素=シリコン)を主な材料とするものではこれ以上の性能向上は難しいだろう」と物理的な限界が指摘されるようになっています。
そこで現在は、Siパワー半導体の課題である “効率化” と “小型化” を実現するものとして、「SiC(炭化ケイ素)パワー半導体」への注目が高まっています。
EV普及を加速させる次世代半導体「SiCパワー半導体」
ここでは、今後需要が急増すると見られる「SiCパワー半導体」について、概要と特徴をご紹介します。
SiCパワー半導体とは
SiCパワー半導体とは、Si(ケイ素)とC(炭素)の化合物である「SiC(炭化ケイ素)」を主材料とする半導体を指します。
1990年代ごろから国内外で研究開発が進められ、1998年には国立研究開発法人新エネルギー・産業技術総合開発機構(NEDO)によって実用化・事業化を目指すプロジェクトがスタート。こうした取り組みを経て量産が実現し、2014年には鉄道車両で実用化されました。
SiCパワー半導体の特徴
SiCパワー半導体は、Siパワー半導体と比べた際に次のような特徴を持ちます。
- より高い電圧や電流、動作温度に耐えられる
- 電気抵抗が生じる箇所の厚さを1/10ほどに抑えられるため、電力のコントロールを行う際のエネルギーの損失が少ない
- エネルギーの損失(通常は全て熱として放出される)による発熱を抑えるための放熱機構を小型・簡略化できるため、機器の小型化が叶う
- エネルギー損失が少ない分、電力をコントロールする機器が効率よく動作するため、一度の充電で走れる距離が長い など
これらの特徴を活かし、Siパワー半導体に代わって、より性能が高く省エネルギーを実現できる “次世代パワー半導体” としてEVの普及を支えることが期待されています。
SiCパワー半導体の今後の展望
続いて、SiCパワー半導体にまつわる市場や各企業の動きと、開発をめぐる今後の展望について解説します。
SiCパワー半導体にまつわる業界の動き
富士経済は2022年5月、パワー半導体の世界市場調査をふまえ、SiCパワー半導体の世界市場は2022年に1,206億円となる見込みであり、さらに2030年には9,694億円に及ぶとの予測を発表しました。
【パワー半導体の世界市場】
| 2022年見込 | 2021年比 | 2030年予測 | 2021年比 |
Siパワー半導体 | 2兆2,137億円 | 110.0% | 4兆3,118億円 | 2.1倍 |
SiCパワー半導体 | 1,206億円 | 159.5% | 9,694億円 | 12.8倍 |
脱炭素化に向けた自動車の電化の進展を背景に、EVをはじめとした電動車や充電インフラの普及に伴ってSiCパワー半導体の需要は大きく拡大し、また低価格化が進むことでSiパワー半導体からの置き換えがさらに進むと見られています。
(参照:株式会社富士経済 プレスリリース「パワー半導体の世界市場を調査」 2022, 05)
このように需要や世界市場の伸びが予測される中、国内でもSiCパワー半導体の生産〜社会実装をめぐってさまざまな動きが生まれてきました。
これまで、SiCパワー半導体を搭載した日本車は少なかったのですが、SiCパワー半導体を搭載した海外製EV車が販売台数を伸ばし、市場の更なる成長が見込まれていることから、その状況は大きく変化してきています。2022年10月にはトヨタ自動車とホンダがEVへのSiCパワー半導体の採用を発表するなど、日本のメーカーの参入も進んでいます。
自動車産業と政府や研究機関とが連携しながら、量産に向けた技術の確立、また日本の半導体産業の復興を目指す動きが進んでいます。
SiCパワー半導体の開発と今後
経済産業省は、SiCパワー半導体を含む次世代パワー半導体の市場予測と技術的な課題をふまえ、次の2つの研究開発目標を設定しました。
- 2030年までに、次世代パワー半導体を使った機器のエネルギー損失を50%低減するとともに、Siパワー半導体と同等のコストを実現すること
- 2030年までに、8インチ(200mm)のSiCウェハ(半導体部品の材料になる板)において、欠陥密度(単位面積あたりの 欠陥=材料面での課題 の数)を1桁以上削減すること
(参照:経済産業省「『次世代デジタルインフラの構築』プロジェクトに関する研究開発・社会実装計画(案)の概要」2021, 07)
これらの目標を実現し、市場獲得や社会実装につなげるために
- エネルギーの損失を減らすために、Siパワー半導体よりも高速に動作する次世代パワー半導体に合った、新しいデジタル制御技術を開発すること
- 「コスト削減に向けてウェハの直径を大きくすること」と「ウェハの材料としての品質を高めること」を両立できる、最適な製造方法を見つけること
- ウェハの欠陥を減らすために、ウェハの製造技術とパワー半導体を使った機器の製造技術の両方を改善すること
などが技術的な課題として残されています。今後、産官学で手を取り合っての取り組みの進展が待たれます。
日機装のシンタリング装置
SiCパワー半導体を基板に接合して電子回路を作るにあたっては、従来のハンダによる接合ではハンダの融点が低い為に高温で使用できるSiCパワー半導体の性能を十分に発揮できないことから、銀や銅を素材とした接合剤を使って焼結(融点よりも低い温度で焼き固めること=シンタリング)する方法の採用が進んでいます。
日機装は、このSiCパワー半導体と基板を焼結接合する工程で用いる装置「3Dシンター」を開発しました。
従来の「メタルプレス方式」では、加圧が平面的なため接合剤が押し出された部分=フィレット部に力がかからず、この部分が脆くなってしまっていた他、チップや基板の高さ・配線パターンに合わせた金型の交換が必要で、段取り変えに多くの時間がかかったり、金型のコストがかかるなどの課題がありました。
一方、3Dシンターで用いられる「3Dプレス方式」では、特殊なゲル状の加圧媒体を使って立体的な加圧が行われます。
これにより、フィレット部にも立体的かつ均一にしっかりと圧力をかけ、欠けを防いで品質を高めることが可能になり、またチップがマウントされた表面の高さに凹凸がある基板でも一括で接合できるため、機器製造の生産性を高められるとともに、ランニングコストも削減できます。
この3Dプレス方式は、日機装がMLCC(積層セラミックコンデンサ)の圧着において業界標準機として広く使用される「温水ラミネーター」を提供する中で培ってきた、“均一加圧・均一加熱” の技術を応用したものです。
また、3Dシンタリング技術を活用し、 EVでニーズが拡⼤している金属基板の製造用3Dプレスも開発しています。
詳しくはこちら> EV でニーズが拡⼤する⾦属基板の製造に最適 特殊ゲルを⽤いた⽴体的なプレス装置「3D プレス」を開発
当社はこれからも、私たちならではの技術力と経験を活かした装置開発を続け、次世代パワー半導体やEVの普及、そしてその先の脱炭素社会の実現に貢献してまいります。
まとめ
脱炭素社会の実現に向け、自動車をはじめとしたあらゆるものの電化において重要な役割を担う部品「パワー半導体」の需要が拡大。中でも、高い性能を持ち省エネルギーを実現できるものとして「SiCパワー半導体」への期待が高まり、開発や社会実装に向けた取り組みが進められています。
日機装は、SiCパワー半導体を用いた機器の製造工程において、SiCと基板の接合を高品質・高効率・低コストで行える「3Dシンター」を開発しました。この装置の展開によってSiCパワー半導体の需要増加への対応に尽力し、脱炭素化に貢献してまいります。
ピックアップ記事
関連記事
-
くらしを豊かに
【日本航空×日機装#2】脱炭素に貢献するCFRP、そして日機装に期待すること
- 航空宇宙事業
- 航空機
- 脱炭素
- CFRP
2025/07/14
-
くらしを豊かに
【日本航空×日機装#1】2050年の空の脱炭素へ、航空業界を牽引するJALの取り組み
- 航空宇宙事業
- 航空機
- 脱炭素
- CFRP
2025/07/09
-
くらしを豊かに
【後編】エンジンナセル部品から翼、胴体部品まで、製品の幅を広げるNikkiso Vietnam, Inc.
- 航空宇宙事業
- 航空機
- CFRP
2024/11/25
-
くらしを豊かに
【前編】エンジンナセル部品から翼、胴体部品まで、製品の幅を広げるNikkiso Vietnam, Inc.
- 航空宇宙事業
- 航空機
- CFRP
2024/10/31