ものづくり
2023/10/04
SiCパワー半導体の品質と製造過程の生産性を高める新技術、「3Dシンター」開発の裏側
- インタビュー
- 半導体
- 技術開発
- 精密機器事業
- インダストリアル事業
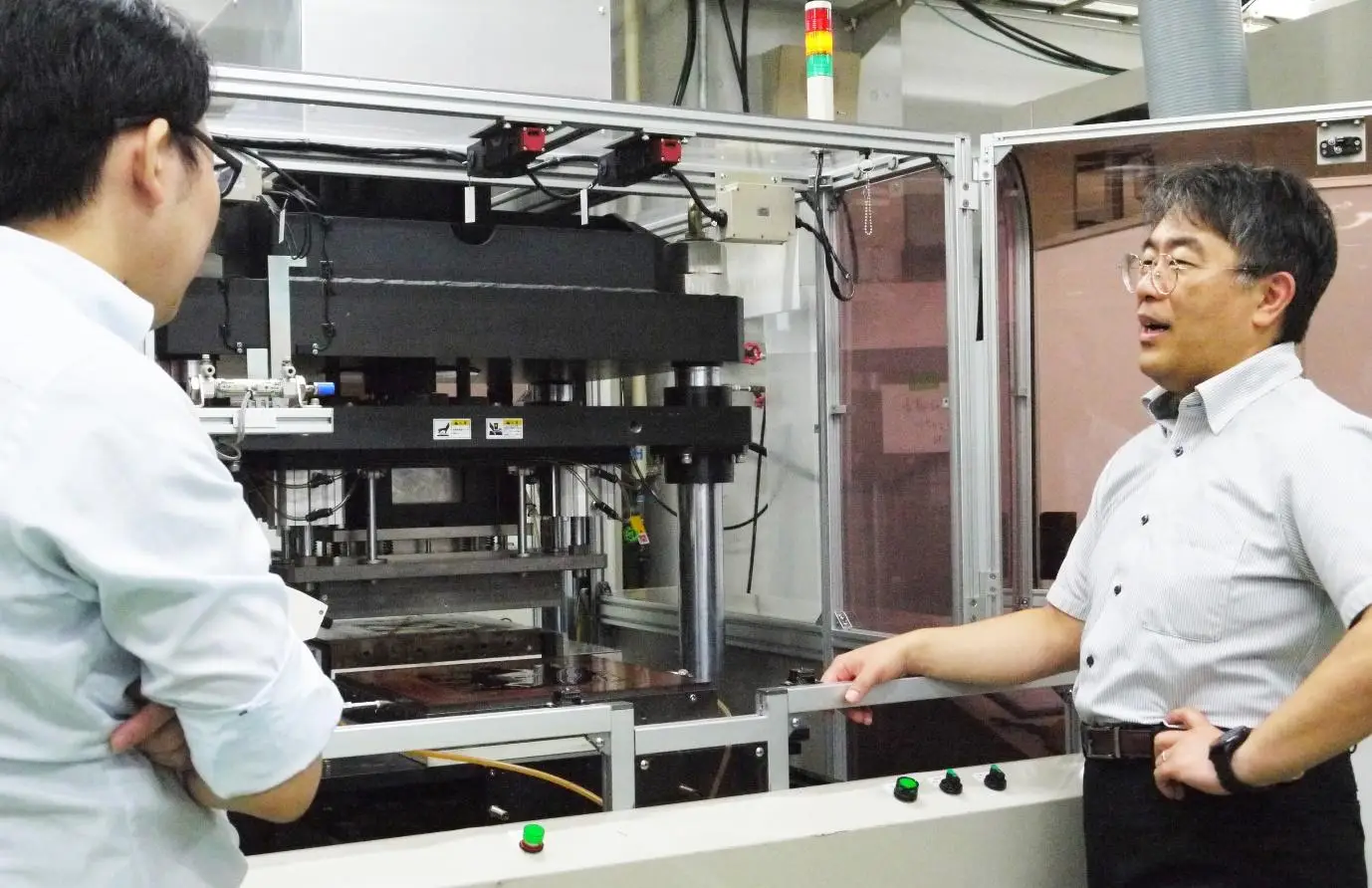
目次
EV(電気自動車)の普及を目指す動きが加速する中、その性能向上に貢献するとして「SiC(炭化ケイ素)パワー半導体」が注目を集めています。
今回は、そんなSiCパワー半導体の製造において重要な役割を果たす装置「3Dシンター」の開発を担う、森氏と井出迫氏にインタビュー。日機装独自の技術を用いた3Dシンターの誕生背景からこの装置ならではの強み、今後の展望について詳しく聞きました。
森 隆博:精密機器技術センター長。技術者として3Dシンターの前身をはじめとした装置の設計・開発・お客様への導入を経験した後、現在は電子部品製造のための生産装置や発電所用水質調整装置などの技術管理を担う。 井手迫 聡:精密機器技術センターにおいて、装置開発やお客様とのテスト対応などを担当する。 (※所属・肩書は取材時点のものです) |
日機装独自の技術を用いた「3Dシンター」で、パワー半導体の品質向上に貢献
――本日はよろしくお願いします。まず「シンタリング装置」とはどのような装置か、ご説明いただけますか。
井出迫:昨今、従来の半導体よりも大きな電圧に耐え、大きな電流を流せる次世代の半導体デバイスとして「SiCパワー半導体」が注目を集めています。
このSiCパワー半導体を製造する際に、銀や銅を素材とした接合材を使って基板上にチップを接合する工程を「シンタリング」といい、シンタリング装置とは、熱と圧力によりチップと基板を接合するためのものです。
――日機装が開発した「3Dシンター」とはどのようなものなのでしょうか。従来の装置との違いも踏まえて教えてください。
井出迫:従来の「メタルプレス方式」は、チップを押す金型が平板になっており、チップを真上から平面的にプレスする方式でした。
これに対して、日機装独自の技術である「3Dプレス方式」を用いた3Dシンターでは、加圧部分に柔らかい特殊なゲル状の加圧媒体(弾性体)を使用しており、基板上のチップを包み込むような形でプレスする仕組みになっています。
――3Dシンターを用いることのメリットとしては、どのようなものがありますか?
井出迫:まず、圧力ムラが解消できることです。
従来のシンタリング装置では、チップの高さによって規定より圧力が高く、もしくは低くなってしまったり、加圧したいエリアの中央と端とで圧力に差が生じてしまったりと、圧力ムラが生じていました。
一方3Dシンターなら、チップの凹凸に追従する形でプレスするため、すべての箇所に均一な圧力がかけられます。「しっかりプレスできていないところがある」「圧力がかかりすぎてチップが割れてしまう」ということがなくなるのです。
たしかに従来の方式でも、チップの形状に応じた金型を使用することで圧力ムラを解消することは可能です。しかし、この方法ではチップの種類ごとに金型を作り替えなければいけません。3Dシンターを活用いただくことで、このような手間と時間を削減できるほか、チップ種別の高額な金型を制作する必要もなくなるため、ランニングコストを大幅に削減できます。
さらに、3DシンターはSiCパワー半導体の強度を高めることにも貢献します。
従来はチップ部分への平面的な加圧のみだったので、チップと基板の間から接合材がはみ出した部分(フィレット部)には圧力がかかっていませんでした。つまり、この端の部分はしっかりと焼き固められていない状態で、ここからチップが剥がれてしまう懸念があったのです。
一方3Dシンターでは、チップ全体を包み込むようにして各方向から圧力がかかるため、フィレット部の強度が高くなり、チップ剥がれのリスクを抑えられます。
市場の動きに先駆けて、新技術を実現したい
――どのような経緯で、この3Dシンターの開発がスタートしたのでしょうか。
森:はじめからSiCパワー半導体向けの装置を開発していたわけではなく、MLCC(積層セラミックコンデンサ)の圧着工程における、水圧を利用した立体的なプレス技術の応用過程で見つけた一つの用途でした。
といいますのも、現在接合材として用いられている「ナノ銀」や「ナノ銅」は、耐熱性や耐久性の高さで注目を集めていた素材。これらの焼結温度は300度を超えることから、今後300度を超える温度でプレスを行う技術が求められそうだと考えていました。実際に、動作環境が高温になるSiCパワー半導体の領域において、かつて主流だった「はんだ」に代わる素材としてナノ銀やナノ銅が活躍するようになっていたのです。
しかし、有機物である弾性体が耐えられるのは200度まで。当初はどうしたら300度という超高温でプレスができる装置を作れるか具体的なイメージはできていませんでしたが、「市場の動きに先駆けて、300度で均一な加圧ができる技術を見出そう」と今回の技術開発が始まりました。
――そこからどのように技術が実現し、3Dシンターの誕生に結びついたのですか?
井出迫:弾性体の素材や金型の構造を工夫しようと考えを巡らせましたが、“凹凸に追従できる柔らかさ” と “熱や圧力への強さ” を兼ね備えた素材や、均一な加圧ができる構造はなかなか見つからず、半年ほど試行錯誤が続きました。そんな中で、偶然のひらめきから生まれたのが「熱をかけたい部分(基板とチップの接合面)だけを温めればいい」という発想でした。
森:金型全体を200度まで加熱する手法から、弾性体を含む金型上部は加熱せず、加圧するワークを300度にまで温度を高める手法に変え、また接合材と弾性体の間に柔らかい断熱層を設ける仕組みに。これによって、弾性体が200度を超える高温になってしまうのを防ぎながら、加圧したい部分に熱がこもる状態を作り、300度でのプレスを実現したのです。
さらに加熱用と冷却用の2つの金型を用意しておいてスイッチさせることで、これまで難しかったプレスをしながら急冷却が可能に。また、プレスを行う中で弾性体の温度が上がってしまうリスクが解消され、実用化に近づきました。
この技術が形になったのは、開発を始めてから2年ほどの時間が経った頃のことでした。そしてテストやデモを進める中で「シンタリングにもこの技術を応用できるはずだ」と気がついたことから、3Dシンターが誕生しました。
――技術開発をしていた時のお二人の思いはいかがでしたか?
森:多くの技術開発は、おぼろげながら構想があって「こうすればいいのではないか」という思いを持ちながら進めますが、今回は実はそれが全くありませんでした。ですので、実現性のあるアイディアに辿り着くまで、どうすべきか思いを巡らせる時間は苦しくもありました。
突破口となった「熱をかけたい部分だけ温める」というアイディアは、お風呂で自分が温まりながらたまたま思いついたんです。そこから、開発が再び加速し始めました。自分が「開発しよう」と言い出したことをやり遂げられてよかったです。
井出迫:私も、お客様のデモやテストに対応する中で「もっと高温でプレスしたい」「より大きな圧力が必要」というご要望をかねてお聞きしており、何とかしたいなと思っていました。今お客様ができずに困っていることを、日機装の装置、ひいては私たちの技術センターで一緒にできるようになればという思いで、開発を進めてきました。
森さんのアイディアは、外出先でたまたま会った時に聞きました。私が全く考えてもいなかったことでしたが、「おー、確かにこれならいけるんじゃないか」と行き詰っていた道が開けた感じがしましたね。
パワー半導体市場が活気づく中国で、デモ拠点を急ぎ設置
――国内での「3Dシンター」のデモ機設置後、2023年1月には上海にデモルームを開設したとのことですが、上海への展開を進めた背景とは?
森:日本以上にパワー半導体市場が活気付いている中国に、装置を試せる場を作ることを急ぐ必要がありました。
特に中国のお客様は、プレゼンだけでは納得してもらえないことが多いです。その場で、パワー半導体のシンタリングが「できる」ということを立証する必要があるため、装置を上海へ持ち込んでデモルームを開設しました。
井出迫:接合材は、本来塗ってすぐに乾燥させてその場でプレスするのが望ましい、生ものと言える素材です。都度現地へ素材を持って行ったり送ったりすることなく、お客様のご要望を受けてタイムリーにデモができる現地拠点が必要でした。
――上海のデモルームの様子やお客様からの反響はいかがですか?
井出迫:デモのニーズはやはり一定数あり、お打ち合わせから素材の準備、条件の決定などを進めながら、週に1〜2件のデモを継続的に行っています。
これまで海外においては資料ベースでのご紹介が中心でしたが、装置の実物を前に大きさのイメージや構成を具体的に知っていただけるようになり、ご好評をいただいています。また、やはりご要望へのタイムリーなご対応ができるという点で「すぐにデモに対応してもらえてよかった」という嬉しいお声もありました。
より多くのお客様のご要望を叶えるために、技術開発は続く
――ありがとうございます。それでは最後に、今後に向けた思いをお聞かせください。
井出迫:装置として形になってよかったという思いはある一方で、まだスタートラインに立ったところなのかなと思っています。デモを進める中で「もっとこうしてほしい」とさらなるご要望もいただいているため、どんどんブラッシュアップを重ねていきたいです。
現在はパワー半導体の大量生産というお客様のご要望を叶えるための装置開発が進んでおり、今後もさらに生産性を高めるための開発を続けていければと思います。
森:これまでの不可能を可能にしたこの新たな技術は、プロダクトアウトの発想で展開しているもののため、ここから用途を作っていく必要があります。
今回ご紹介したナノ銀やナノ銅、さらに次の段階では発熱量の大きい部品に使われる「放熱基板」への適用を目指して……と、より多くのお客様のご要望を満たすべく用途開発にチャレンジしていければと思います。
ピックアップ記事
関連記事
-
ものづくり
日機装の技術を守り、未来へつなげる。存在感を増す「知的財産室」の役割と新たな挑戦
- インタビュー
- 技術開発
2024/12/04
-
ものづくり
【JAXA×日機装#3】ロケットと水素航空機、ポンプ視点で見た違いは?
- インダストリアル事業
- ポンプ
- 水素
- 航空機
- 脱炭素
- 技術開発
2024/11/06
-
ものづくり
【JAXA×日機装#2】液化水素って、どんな性質?「極低温」という難敵に立ち向かうには
- 水素
- 脱炭素
- 航空機
- ポンプ
- 技術開発
- インダストリアル事業
2024/10/09
-
ものづくり
【JAXA×日機装#1】水素航空機向けポンプ性能試験の舞台、角田宇宙センターってどんな施設?
- インダストリアル事業
- 水素
- 脱炭素
- 航空機
- ポンプ
- 技術開発
2024/10/01