ものづくり
2024/06/19
小型機の量産、航空機の電動化…未来の空に向けた日機装の研究開発は?
- CFRP
- インタビュー
- 人工衛星
- 技術開発
- 航空宇宙事業
- 航空機
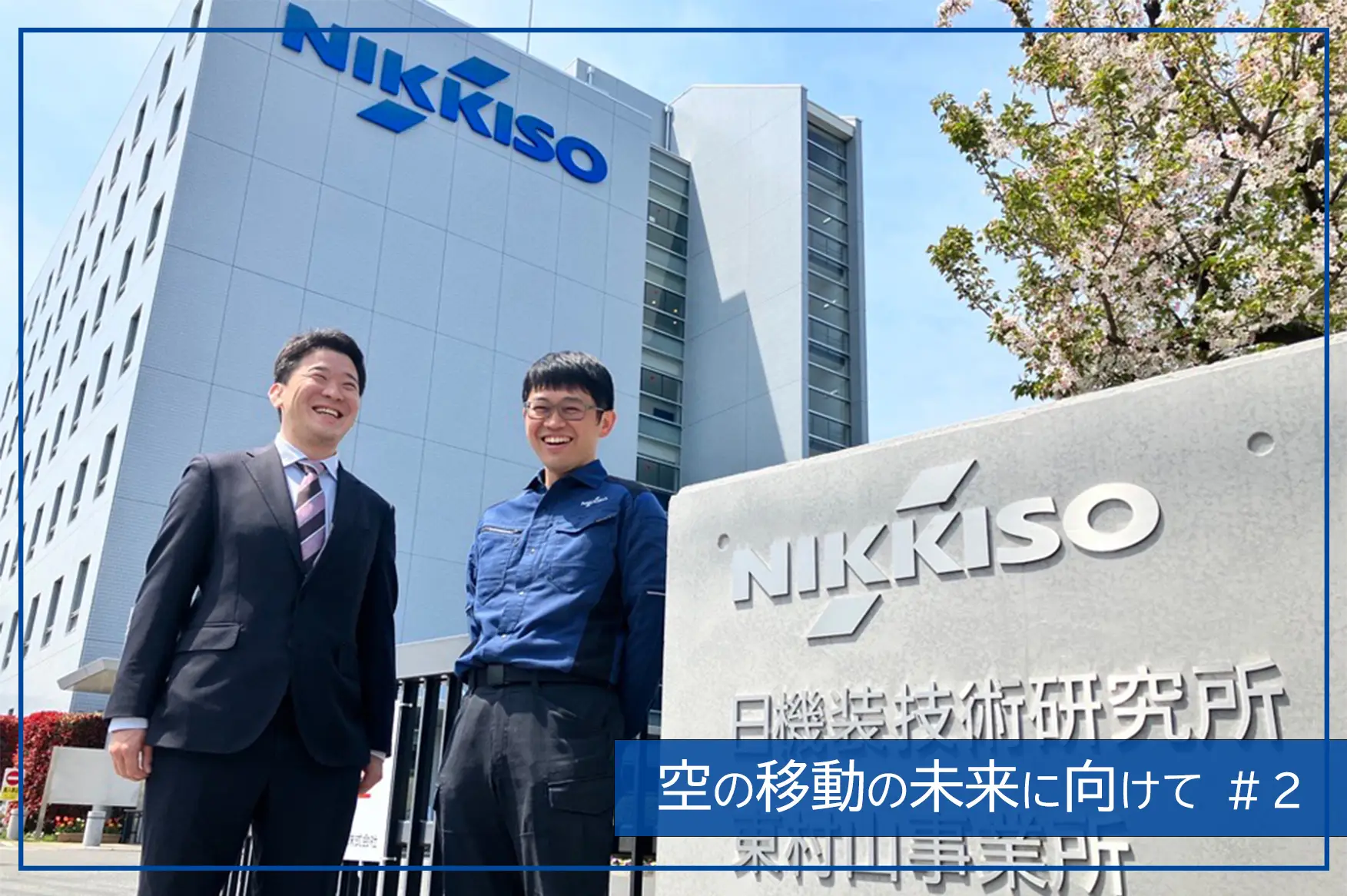
目次
進化する航空機や新たな空のモビリティの誕生に向けた日機装 航空宇宙事業の歩みと挑戦をご紹介するシリーズ「空の移動の未来に向けて」。第2回目となる今回は、技術者の目線を通じて、変革期を迎える航空宇宙業界にどのように対応していくか迫ります。
今回は、航空宇宙事業本部の航空宇宙技術センターで技術開発を担う大岩 亮三氏と渡邊 勇輔氏にインタビュー。現在取り組んでいるテーマや研究開発にかける思いを伺い、変革期を迎える航空宇宙業界において、日機装はどんな挑戦をしているのかに迫りました。
大岩 亮三:2006年入社。カスケードの設計開発業務を経て、現在は航空宇宙技術センター技術第一部 研究開発グループ グループリーダーとして開発の取りまとめと推進を担う。 渡邊 勇輔:航空機の構造設計に携わった後、2020年入社。航空宇宙技術センター技術第一部 研究開発グループに所属。速硬化性樹脂に関する研究チームに所属し、近年では新技術獲得に向けた取り組みにも携わる。 ※所属・肩書は取材時点のものです |
航空宇宙業界の市場変容に対応するべく、研究開発を推進
――本日はよろしくお願いします。まずは、お二人が所属する航空宇宙技術センターの概要からご説明いただけますか。
大岩グループリーダー
大岩:日機装の航空宇宙事業は、「CFRP(炭素繊維強化プラスチック)」という複合材料を用いて航空機や衛星向けの部品を製造しています。この中で航空宇宙技術センターは、新しい製品の量産に向けた立上げ、認定対応、工程の維持管理や、より良い製造法を確立するための技術開発に取り組む組織です。
我々が成形加工技術に強みを持つCFRPは、「軽くて強い」という特徴がよく知られています。航空機に採用すると、機体の重量が減るので、燃費の向上に貢献できます。また、金属と比較して疲労強度(※繰り返し掛かる力に対する強度)にも優れており、最新の機体であるボーイング787やエアバスA350は、機体の約50%にCFRPが使われています。
当社の主力の航空機部品「カスケード」
――CFRPを成形加工するにあたって、特にどのような点が難しいのでしょうか。
大岩:強度な部品をつくるために重要となるのが、繊維の向きです。これを、複雑な形状でも設計通りに配向するのはとても難しいのですが、日機装はこの点において強みがあります。そのため、CFRPを使って複雑な形状のものを複数の部品に分けることなく、一体成形できるのです。
――現在はどのような方針を掲げて研究開発に取り組んでいるのでしょうか。
大岩:現在は、「生産性の向上」「サステナブル」「付加価値の追加」の3つのキーワードを軸に研究開発を進めています。
――そうしたキーワードにフォーカスするようになった背景を教えてください。
大岩:背景にあるのは、航空宇宙業界で見られるさまざまな市場環境の変容です。
例えば、新型コロナウイルス感染拡大を経て主な需要が大型機から中小型機に移り、その分求められる機体の製造量が増えました。
また、「eVTOL」と呼ばれる新たなモビリティが登場したり、環境配慮への社会的な要請が高まる中で、航空機の電動化や航空燃料としての水素の活用、資源の循環を考えた部品開発などの動きも見られたりしています。それに伴い、今後機体やエンジンの形状が変わっていくことも予想されており、あらゆる観点で航空宇宙業界は変革期を迎えているといえるのです。
こうした状況をふまえ、需要に応え得る製造量を担保できるよう生産性を高めること、環境に優しいサステナブルな素材や製造方法を考えること、そして市場の変容や競争の激化に対応できる、より機能的な部品の確立に向けて取り組みを進めています。
――具体的にどのような研究テーマに取り組んでいますか?
大岩:一つは、部品製造におけるサイクルタイムの短縮です。現在は、主にオートクレーブ(圧力容器)を使って樹脂を加熱・加圧して硬化させる「オートクレーブ成形」という方法で部品の成形を行っています。
この成形法は、CFRPの特性、品質を担保しながら大量(バッチ)生産ができるメリットがありますが、一方で加圧・加熱するため成形に時間がかかるという課題があります。また、オートクレーブを長時間運転すると、熱エネルギーを大量に消費するため、サステナビリティの観点からも好ましくありません。
――オートクレーブ成形が抱える課題に対して、どのような解決策を検討していますか。
オートクレーブ
大岩:生産サイクルの時間を短縮し、“安定的な大量生産” と “環境負荷の低い製造工程” を実現するため、以下の2つのアプローチを取っています。
- オートクレーブ成形の改良
硬化時間が従来の樹脂より短いもの(速硬化性樹脂)を使う+樹脂を素早く高温にできるようにオートクレーブの加熱法を変える。 - オートクレーブ成形以外の成形法の確立
従来の樹脂(熱硬化性樹脂)とは異なる性質の樹脂(※熱可塑性樹脂)を使う+材料を金型に入れて圧縮する「プレス成形」という方法を採用し、短時間で効率的に樹脂を硬化させる
※熱可塑性樹脂は加熱すると柔らかくなり、冷やすと硬くなる性質がある。高温に熱した金型で素早く材料を軟化させて形づくり、すぐ冷却することで成形できる。
こうした取り組みは、同じくサステナビリティを重視するエアバス社との共同開発のテーマでもあります。
日機装は2020年、エアバス社から「アウターリング」というエンジン周辺部品の共同開発パートナーに選ばれました。このプロジェクトの中で、日機装は
- 新技術の採用: オートクレーブに代わる新しい硬化手法を採用することで製造コストを削減
- 新素材の採用: 速硬化性樹脂を活用し、製造時間を短縮
に取り組み、デモ試験機用製品として納期通り納めました。
速硬化性樹脂に関する技術開発はもともと日機装で続けており、「一緒に新技術を使った部品開発を」とエアバス側に提案した結果、この共同開発が立ち上がりました。2021年には、別の部品でも共同開発パートナーに選出されています。
CFRPが持つ難燃性(燃えづらさ)は、素材としての強みである反面、焼却処理を難しくしており、現在ではそのほとんどが埋め立て処理されてしまっています。そのため、環境配慮の観点から現状を改善するために、使用済みのCFRPを資源として循環させる方法や、製造過程で出る端材を有効活用する方法なども模索しています。
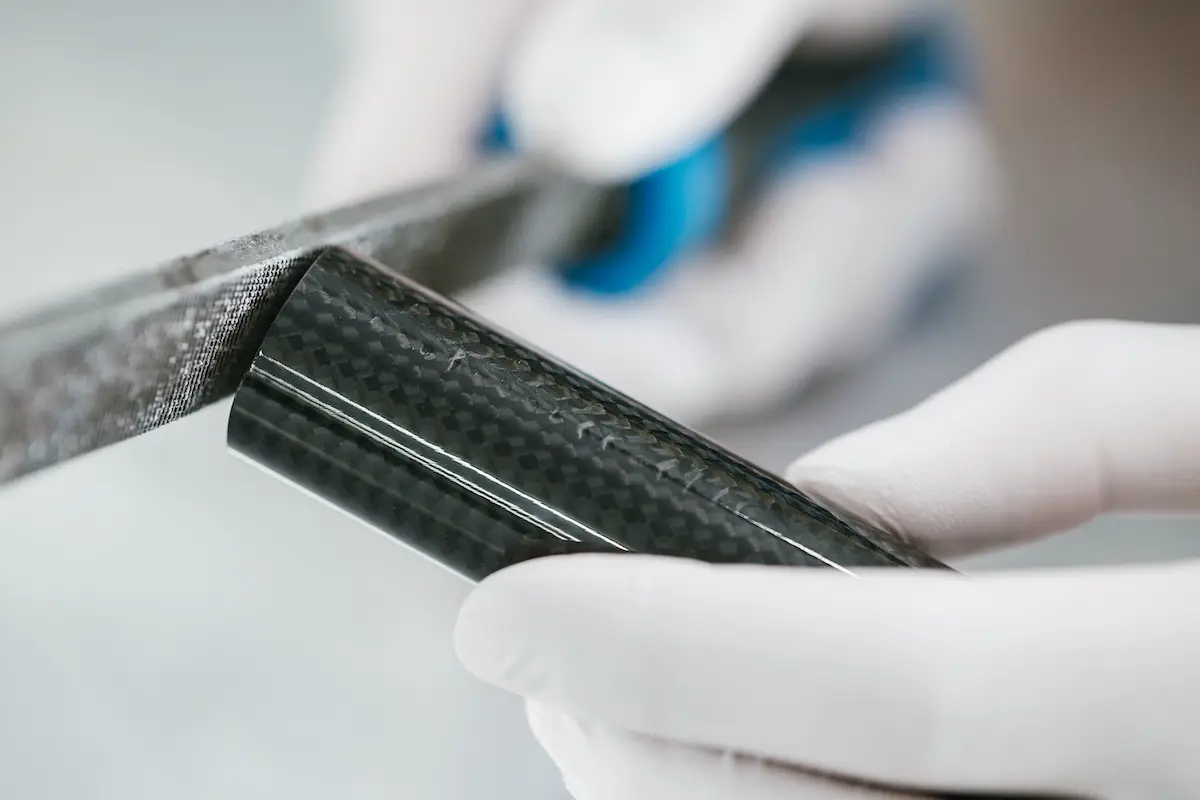
次世代を見据えて新規技術の芽を探す「N-SEARCH」
渡邊氏
――航空宇宙事業本部内で、“次世代に向け新規技術の芽を探す” ことを目的としたチーム「N-SEARCH」が活動していると伺いました。この「N-SEARCH」について、概要をお聞かせいただけますか。
渡邊:大岩からお伝えしたようなさまざまな市場変容を背景に、当社が航空宇宙業界に参画し、発展するきっかけとなった航空機部品「カスケード」に次ぐ新たな技術の獲得を目指そうと「N-SEARCH」が発足しました。
――具体的な活動内容を教えてください。
渡邊:主な活動内容は、次世代に向けた新規技術獲得のための情報収集及び新規開発テーマ立案に向けた初期検証の実施となります。開発テーマとして取り扱うかどうかを判断するための材料集め的な位置付けと考えております。基本的には航空宇宙分野をターゲットとしているものの、他事業部の技術者とも対話をしながら他分野への展開の可能性を探るなど、広範囲に活動をしています。
――どのような体制で活動を進めているのでしょうか。
渡邊:航空宇宙業界全体の商流を知る営業部門、当社ならではの技術を知る設計・製造部門などさまざまな部署から任命されたメンバーが「N-SEARCH」に参加し、それぞれの知見を持ち寄って活動を進めています。
――現段階で調査や検証に着手している具体的なテーマがあれば教えてください。
渡邊:現在視野に入れているのが、当社が強みとするCFRPにさらなる価値を付与した「機能性複合材料」の開発です。
軽くて強度が高く、疲労特性や耐候性、耐薬品性、熱伝導性に優れるなどさまざまな強みを持つCFRPについて、①今ある特性をさらに伸ばす ②+αの特性を付与する ③欠点を補う、など、さらに強みを持たせることで付加価値を高め、航空宇宙業界を中心としつつ他業界への適用範囲を広げたりすることを目指しています。本要素研究については、広島大学、東北大学との共同研究にて検証を行っております。
より多くのお客様に日機装の技術や製品が届くように
――市場シェア90%以上を誇るカスケードをはじめ、その技術力が世界的に高い評価を得ている現状にとらわれることなく、未来を見据えて挑戦し続けていることが印象的でした。お二人は今、どのような思いで研究開発に取り組まれていますか?
渡邊:私は日機装に入社して3年ほどになりますが、「将来に向けてこんなことをやってみたい」と思うテーマに挑戦できる機会を頂けることと、常識や日機装における技術的な蓄積にとらわれずに挑戦できること、失敗しながら学べる環境にいられることをありがたく思っています。
大岩:グループを統括する身としても、前例のない取り組みがさまざまあり、非常にチャレンジングな環境だと感じています。そうした中、昨年CFRPと異なる性質を持つ「CFRTP」を用いた独自の成形技術を確立できたのは私たちにとって大きな進歩でした。この成果を次に活かし、カスケードに次ぐ主力製品の開発に繋げていきたいですね。
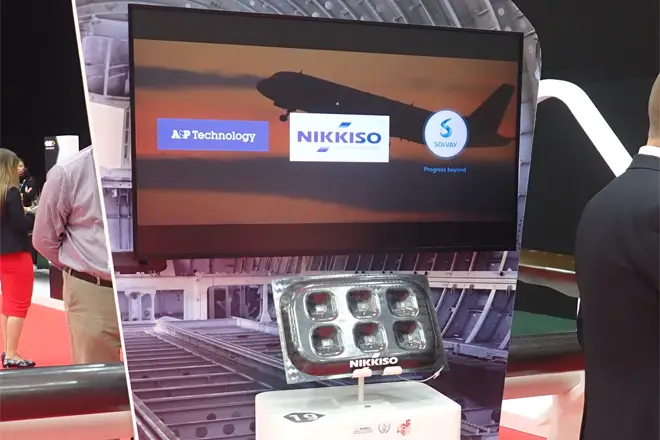
――ありがとうございます。それでは最後に、今後に向けた抱負をお聞かせください。
渡邊:主力製品であるカスケードはもちろん、その他の航空宇宙関連製品や新たな分野の技術なども含めて、日機装が手がけたものをより多くのお客様に使っていただくことを目標として研究開発に取り組んでいきたいです。
大岩:航空機、そして航空宇宙業界は、これからも「より速く、より快適に、より環境に優しく」を軸として変化を続けていくでしょう。こうした市場の動きをしっかりと捉え、メンバーの高いモチベーションを維持するとともに、これまで培ってきたお客さまとの信頼関係を大切にしながら、今後も研究開発を推進していきたいと思っています。
研究開発グループはまだまだ小さな組織。取り扱うテーマや活動の幅を広げるためにも、組織拡大や他事業部門との連携強化によって、社会に貢献する技術を生み出せる体制を築いていきたいです。
ピックアップ記事
関連記事
-
ものづくり
日機装の技術を守り、未来へつなげる。存在感を増す「知的財産室」の役割と新たな挑戦
- インタビュー
- 技術開発
2024/12/04
-
ものづくり
【JAXA×日機装#3】ロケットと水素航空機、ポンプ視点で見た違いは?
- インダストリアル事業
- ポンプ
- 水素
- 航空機
- 脱炭素
- 技術開発
2024/11/06
-
ものづくり
【JAXA×日機装#2】液化水素って、どんな性質?「極低温」という難敵に立ち向かうには
- 水素
- 脱炭素
- 航空機
- ポンプ
- 技術開発
- インダストリアル事業
2024/10/09
-
ものづくり
【JAXA×日機装#1】水素航空機向けポンプ性能試験の舞台、角田宇宙センターってどんな施設?
- インダストリアル事業
- 水素
- 脱炭素
- 航空機
- ポンプ
- 技術開発
2024/10/01