ものづくり
2023/06/08
CFRTPで環境にやさしく、効率的に航空機用部品を造る|航空機分野における脱炭素化への取り組み
- インタビュー
- 航空機
- 技術開発
- 航空宇宙事業
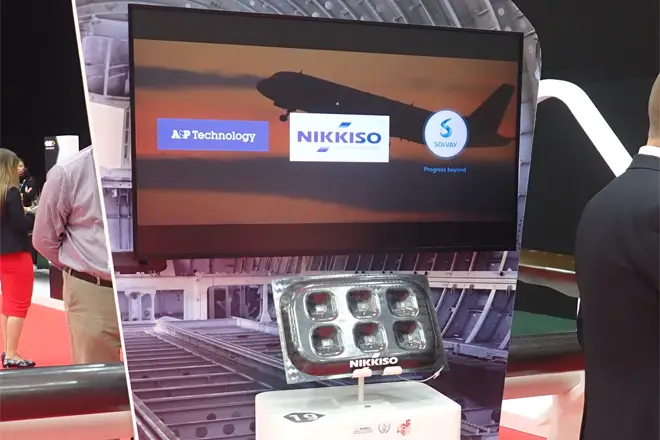
目次
航空分野においても2022年に長期目標として「2050年までのカーボンニュートラル実現を目指すこと」が掲げられ、さらに法改正や基本方針の策定が進められるなど、脱炭素化を目指す取り組みがこれまで以上に加速してきました。
そうした中、航空機製造分野においても環境負荷を低減できる材料として、「CFRTP(熱可塑性炭素繊維複合材)」への注目が高まっています。
今回は、日機装でCFRTPの成形技術の研究開発を担う齋藤氏にインタビュー。環境負荷軽減の観点をふまえながら、CFRTPの特徴と日機装が確立した成形技術について詳しく聞きました。
齋藤 浩一郎:自動車用エンジン部品の開発及び設計に携わった後、2020年入社。航空宇宙事業本部 技術センター技術部にて、研究開発を担当する。(※所属・肩書は取材時点のものです) |
次世代の構造材料として期待が高まる「CFRTP」
――本日はよろしくお願いします。まずはCFRTPとはどのようなものか、概要からご説明いただけますか。
齋藤:まず、航空機の構造材料は、軽量化を図るために金属から炭素繊維複合材への置き換えが進んできました。炭素繊維複合材には、CFRP※1と呼ばれる「熱硬化性樹脂」に強化材として炭素繊維を加えたものと、CFRTP※2と呼ばれる「熱可塑性樹脂」に炭素繊維を加えたものの2種類がありますが、現在、航空機の構造材料として主流になっているのはCFRPです。CFRPは熱を加えると硬化する「熱硬化性樹脂」、対してCFRTPは熱を加えると軟化する「熱可塑性樹脂」を使用しているため、CFRTPは一度硬化しても熱を加えれば自由に変形できるという特徴があります。
CFRPは一度焼き上げると形を変えられないクッキー、CFRTPは温度に応じて形を変えられるチョコレートのようなもの……とイメージしていただくと分かりやすいでしょうか。
※1:CFRP=Carbon Fiber Reinforced Plastics
※2:CFRTP=Carbon Fiber Reinforced Thermo Plastics
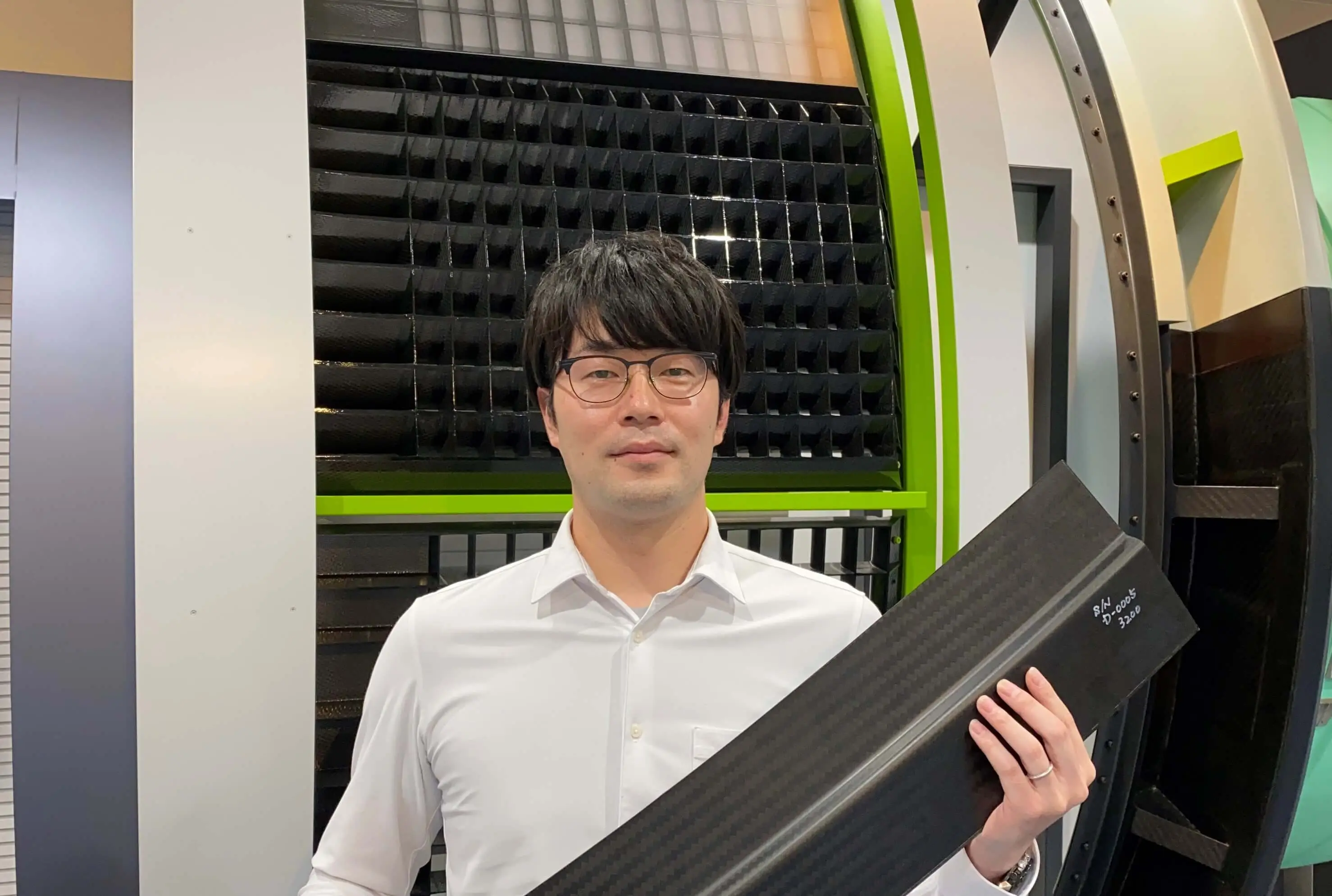
――航空機分野において環境意識が高まる中で、CFRTPが注目されているのはなぜですか?
齋藤: 熱可塑性という特徴から、比較的リサイクル性が高いことが挙げられます。先ほどもお話した通り、CFRTPは熱可塑性の素材。使用後の部品に熱を加えれば形を変えられるので、別の部品に再利用することもできるんです。そのため、一度使った部品を使い捨てすることなく、資源を大切にできる材料として研究開発への期待が高まっています。
また、従来のCFRPは保管時に樹脂が硬化してしまわないよう、マイナス20℃という極低温の環境を用意しなければいけませんでした。そのような環境でも少しずつ化学反応は起き、硬化が進んでしまうので、素材としての消費期限が存在したんです。
一方CFRTPは常温での保管が可能で、常温の環境下では状態が変化せず、素材としての性能を発揮します。CFRPのように特殊な冷凍庫を用意したり、消費期限を管理したりせずに済むので、管理コストを大幅にカットできます。また、保管時に電力などのエネルギーを必要としないのも注目されている要因です。
――サステナビリティの観点で、従来の構造材料と比べてより優れていると。
齋藤:そうですね。また、成形した部品の一部に熱を加えて軟化させれば、金属の溶接と同じように、ボルトや接着剤を使わずに別の部品を接合できる「溶着」が可能です。これによって生産が効率化できることに加え、ボルトを使わないとなるとその分重量が軽くなりますから、機体の軽量化や、それに伴う燃費向上、製造時に必要なエネルギーの低減によるCO2削減につながる点もCFRTPならではの魅力ですね。
――そうした特徴をふまえ、CFRTPはどのような場所で用いられているのでしょうか。
齋藤:航空機や自動車のボディー等の一部の部品でCFRTPが採用され始めていますが、今や航空機の機体の50%(重量比)を占めるといわれているCFRPに取って代わる……というほどには、まだ活用が進んでいないのが現状です。
――現状、CFRTPの活用がまだ進んでいない理由はどういった点にありますか?
齋藤:最大の理由は、成形についての技術的なハードルの高さにあります。CFRPは成形時の温度が120℃~170℃ほどであるのに対して、航空機で求められる高性能なCFRTPの成形温度は高いもので400℃ほど。この高温状態で金型内の材料に温度差や圧力差が生じないようそれぞれを均一に維持する必要があるので、成形が非常に難しいんです。
また、温度や圧力の管理がしやすい従来のオートクレーブを使用した場合、成形温度が高い分、成形時に使用する副資材や設備自体も高温に耐えられるものでないといけなくて。そのため、CFRPと比べてコスト面での負担が大きくなりやすいことも普及がなかなか進まない理由のひとつだと思います。
環境負荷が小さく、製造リードタイムを大幅に削減。CFRTPを用いた独自の成形技術を確立
――日機装では、そんなCFRTPを用いた独自の成形技術を確立し、航空機部品の開発プロジェクトで「JEC Composites Innovation Awards 2023(※)」ファイナリストに選出されたと伺っています。まず、プロジェクトの概要についてお聞かせください。
(※JEC Composites Innovation Awards:メディア・イベント団体JECグループ主催。複合材料の可能性を最大限に発揮した最先端かつ創造的なプロジェクトに授与される賞 / プレスリリースより引用)
齋藤:CFRTPを活用した航空機部品の開発の一環として、日機装が2020年頃から取り組み始めたプロジェクトです。
CFRPなど熱硬化性の材料で、強度や剛性、衝撃吸収性に優れた “軽くて強い” パネル状の部品を製造するためには、ハニカム材(蜂の巣状の補強部材)を使用するのが一般的です。航空機の床材や各種パネル類など、ハニカム材は航空機用部品として多用されています。ただ、このハニカム材はコストが高いうえに、高い精度で加工することが難しいなどの問題がありました。
そこで今回のプロジェクトでは、「高コストなハニカム材を用いることなく、軽くて強い航空機部品を作る」ことをテーマに取り組んでいた研究開発の一環として、さまざまな方向からの荷重に耐えられる航空機の一次構造部品などに使用する補強用パネルを考案。環境負荷が少なく製造リードタイムを削減した成形方法を実現したことで、入選できました。
――日機装が確立した成形技術の特長は、どのようなところにあるのでしょうか。
齋藤:炭素繊維を切り刻むことなく連続した状態のまま用いることで、強度を高めつつ、環境負荷が少なく製造リードタイムも削減できる方法で、複雑な形状のパネルのプレス成形方法を確立したことがポイントです。
これまでCFRPの成形において日機装が採用してきた「オートクレーブ(Autoclave)成形法」では、オートクレーブと呼ばれる圧力容器を用いて加圧・加熱を行い、成形します。
この方法ではCFRP製部品の成形におよそ4〜10時間かかる(炭素繊維の種類や形状によって異なる)のが一般的で、さらに高い成形温度が求められるCFRTPと相性がよいとは言えません。また、CFRTPの成形には化学反応を伴わないので、高温を長時間維持する必要もありません。
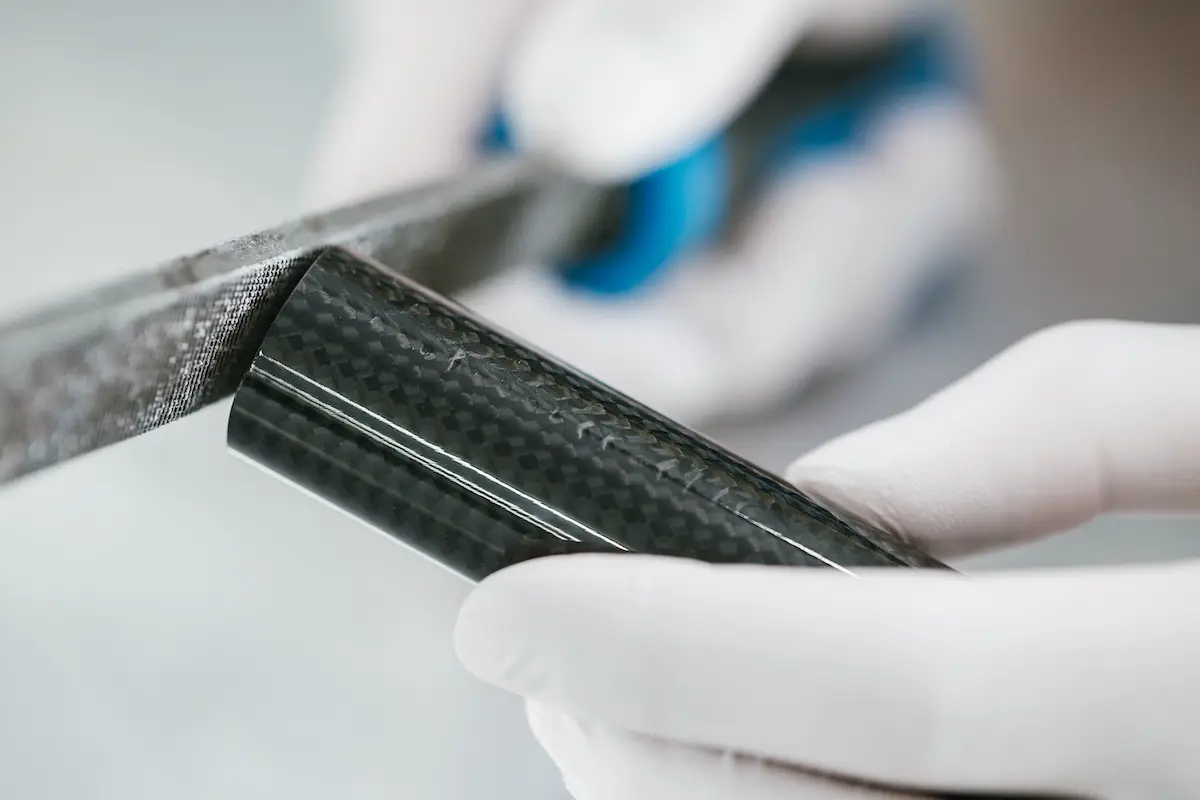
対して、今回開発した上下の金型の間にシート状の材料を配置し、上下型を閉じて加熱・加圧することで成形する「プレス成形法」は、高温に熱した金型で材料をすばやく軟化させて部品を形作り、すぐに冷却することで成形品が得られます。CFRTPと相性がよく、これによって部品製造リードタイムが7分の1ほどに短縮できました。
また、単に成形時間が短縮できるだけではなく、廃棄物量や製造コストが削減できるところも、今回当社が開発したプレス成形技術の特徴です。
――今回日機装が確立したプレス成形法では、従来の方法と比べて成形に伴う廃棄物をどれほど減らせるのですか?
齋藤:オートクレーブ成形法で部品を成形する際は、真空状態を作るためにフィルムや接着テープなど多くの副資材が必要ですが、プレス成形法は金型のみ。製造時の廃棄物はほとんどゼロと言ってよく、環境面でもメリットがあるんです。
また、部品を成形する際は、オートクレーブ成形法でもプレス成形法でも、少し大きめのサイズで成形した後に、部品外形を大きく削って整えることが一般的です。しかし、今回日機装が確立した成形技術は、ぴったりのサイズで成形できる方法を適用しているため、成形後に大きく削る必要がなく、廃棄物量や製造コストが削減できるところも特徴です。
――製品化に向けて、今後どのような課題を解決していこうとお考えですか?
齋藤:現在はまだ試験段階なので、量産に向けてまずは「より品質の安定した部品をより速く造ること」を突き詰めていきたいです。そして、今回作った補強用パネルとは異なる形状や大きさの部品でも成形できるようにすることで、技術の幅を広げていきたいと思います。
――日機装独自のプレス成形法によるCFRTP製の一体型高剛性構造部材(ブロッカードアの補強用パネル)が、4/25〜4/27にパリで開催された「JEC World 2023」に展示されたとお聞きしました。
齋藤:はい。「JEC Composites Innovation Awards 2023」ファイナリストとして、主催者が設置するブースで成形品を展示しました。また、今回の取り組みのパートナー企業であるSOLVAYとA&P Technologyのそれぞれのブースにも出展しました。
ファイナリスト選出を受けて各ブースの最も目立つ場所に展示していただいたこともあり、注目度は高かったですね。航空機を製造する各社の方々と意見交換した際も、ポジティブな意見を多くいただくことができました。
また、駆け出しの開発技術なので、今後に向けた具体的なステップアップについてのアドバイスも多く、私たちの技術が期待してもらえていることを実感する機会となりました。
独自技術をかけ合わせ、“私たちにしかできない部品造り”を
――ありがとうございます。それでは最後に、ここまでの研究開発の振り返りと、今後日機装の技術部として実現したいことをお聞かせください。
齋藤:これまで40年にわたってCFRP製の部品をオートクレーブ成形法で製造してきた日機装にとって、今回のプロジェクトは新たな材料を使った新たな製造技術獲得への大きな挑戦でした。
トライアンドエラーを何度も繰り返しながら部品を形にすることができ、結果として「JEC Composites Innovation Awards2023」ファイナリスト選出という評価をいただいたことをとても嬉しく思っております。「自分たちは面白いことに挑戦していたのだ」という自信につながりましたね。
今後は、CFRTP製の部品の量産や普及に向けた技術改良を進めるのはもちろんのこと、当社が独自で取組んでいる溶着技術を確立し、日機装がこれまで培ってきた技術をかけ合わせながら、“私たちにしかできない部品づくり” に取り組んでいきたいと思います。
ピックアップ記事
関連記事
-
ものづくり
日機装の技術を守り、未来へつなげる。存在感を増す「知的財産室」の役割と新たな挑戦
- インタビュー
- 技術開発
2024/12/04
-
ものづくり
【JAXA×日機装#3】ロケットと水素航空機、ポンプ視点で見た違いは?
- インダストリアル事業
- ポンプ
- 水素
- 航空機
- 脱炭素
- 技術開発
2024/11/06
-
ものづくり
【JAXA×日機装#2】液化水素って、どんな性質?「極低温」という難敵に立ち向かうには
- 水素
- 脱炭素
- 航空機
- ポンプ
- 技術開発
- インダストリアル事業
2024/10/09
-
ものづくり
【JAXA×日機装#1】水素航空機向けポンプ性能試験の舞台、角田宇宙センターってどんな施設?
- インダストリアル事業
- 水素
- 脱炭素
- 航空機
- ポンプ
- 技術開発
2024/10/01